Manufacturing Process of Aluminium Solar Panels Frame
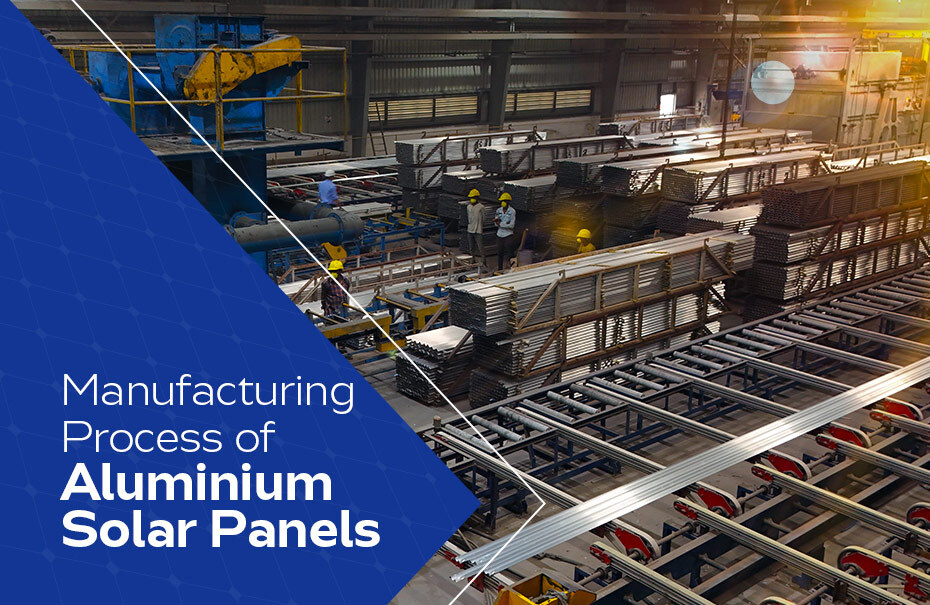
The manufacturing process of aluminum frame for solar panels significantly improves solar energy reliability and efficiency. Aluminum is the most preferred material because it is strong, doesn’t rust, and is lightweight. The strong frames that manufacturers make from cut and treated metal hold up the panels and make them easy to place.
The modern look of solar panels comes from these frames as well. Aluminum solar panels are leading the way for more environmentally friendly energy options with their well-designed manufacturing process.
How is the Manufacturing Process of Aluminum Solar Panels Frame carried out?
The manufacturing process of aluminum solar panels frames involves several key steps that ensure the frames are durable, strong, and capable of supporting solar panels for years to come. Each step in the process is carefully designed to enhance the frame’s strength, appearance, and long-lasting performance in all types of weather.
1.
Selection of Raw Materials for Solar Frame
The first step is to choose the right raw materials for solar panel. Aluminum is the main material used for solar panel frames because it is lightweight, strong, and resistant to rust and corrosion. But all aluminum isn’t the same in general. We only use high-quality metal to make our frames so that they will last a long time. Before the material is approved for use, it is carefully checked for any flaws or pollutants that could weaken it.
After the initial inspection, the aluminum is cleaned to remove any surface contaminants, like oxides or residues, that could hinder its processing. This step of cleaning is very important because the metal needs to be in great shape for the frame to last a long time and keep its shape. How well the frame protects the solar cells from bad weather depends a lot on how strong and good the material is.
2.
Extrusion Die
Once the raw aluminum is ready, it is time for the extrusion process. During this step, the aluminum is heated to a high temperature until it becomes molten. Once molten, it is driven through an extrusion die—basically a mold—that forms the aluminum into long, uniform profiles. The structure keeping the solar panels in place will have this profile.
The molten aluminum flows through the die and emerges as long sections of the solar panel frame. Although these parts cool rapidly to harden the aluminum, at this stage the material is still soft and needs further treatment to straighten it out and idealize its form.
3.
Shot blasting
Shot blasting comes next after the metal has been extruded. This procedure requires surface blasting of the metal frame with tiny Stainless Steel grains. Like a polishing agent, the SS smooths out any sharp edges and leaves the surface clean, matte appearance. Any little flaws left over from the extrusion process may also be removed by shot blasting.
Feature approximation involves giving the cover a form and also fine-tuning the surface for the next important processing phase: anodizing. Shot blasting is capable of removing any contamination and giving a smoothened finish, thus improving the conditions for aluminum, which would then take on the anodized coating with a further protective provision to seal the whole so that corrosion or normal environmental influences do not attack or set in.
4.
Anodizing
Anodizing a very important step in the making of aluminum solar panels. This is a chemical process where the aluminum frame is covered with a highly protective oxide layer that is generally done under electrolysis solution. It is this layer, therefore, that adds to the resistance of the frame so corrosion can be avoided; hence the years of resistance through rain and wind and sun will further guarantee its durability.
Before the anodizing process, the aluminum frame is put into the solution and an electric current is run over it. When the aluminum combines with the fluid, a thick layer of oxide forms on its surface. Anodizing not only makes the frame more resistant to rust, but it also gives it a smooth, finished look that makes it look better. The aluminum finish helps protect the solar panel structure from rust, scratches, and wear, so it will last for a long time and keep working.
5.
Fabrication
In the final stage, the frames are machined to precise dimensions and specifications as per the customer’s drawings. This process includes cutting, crimping, and clip-inserting operations. Rigorous quality inspections are conducted to ensure the frames are reliable, durable, and suitable for solar panel applications.
Powering the Solar Industry with Durable and Efficient Aluminum Frames
In conclusion, Vishakha Renewables is among the leading aluminum solar frame manufacturers in India. With over 30 years of experience at the forefront of the solar industry, we offer top-quality products that ensure durability and efficiency, making us the perfect partner to provide the raw materials you need to succeed in your solar manufacturing business.
The anodized coat has not only 15+ Micron Anodizing Thickness. It has been manufactured from high-grade Aluminum Alloy 6063 and 6005. The increased strength of the frames was promoted by this coat that acts as an anodizing shield, which not only enhances the look of the frame, but also provides it with resistance to rust and corrosion protection, forcing them to withstand strong weather conditions.
Our commitment to quality and innovation makes us the go-to choice in the solar manufacturing space. If you want your solar panels to stand the test of time and weather, you know where to turn.